Introduction
Personal protective equipment (PPE) plays a crucial role in safeguarding human health, especially in clean working environments such as healthcare, food processing, and manufacturing, or in high-risk workplaces like construction sites and chemical plants.
According to a report from Mordor Intelligence, the global PPE market is expected to reach $27.43 billion in 2024 and grow at a CAGR of 13.26% to $51.13 billion by 2029. North America and Europe account for approximately 70% of the market share, indicating that the U.S. is one of the largest PPE consumers globally. However, it also imposes stringent quality and import process standards.
In recent years, many Vietnamese businesses and companies from other countries have struggled to export PPE to the U.S. due to failure to meet stringent safety, technical standards, licensing, and customs regulations. This has led not only to financial losses but also to reputational damage in the international market.
This article will analyze four main reasons why PPE shipments are rejected by the U.S. and provide detailed guidance on how to resolve these issues to ensure smooth export processes.
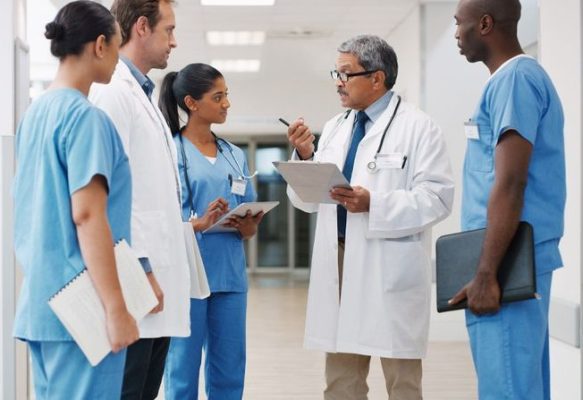
4 Main Reasons Why PPE Shipments Are Rejected by the U.S.
PPE Fails to Meet Quality Standards
The U.S. enforces very strict standards for PPE to ensure user safety. Some critical filtration performance criteria include:
- BFE (Bacterial Filtration Efficiency): For medical masks, the minimum level must reach 95% or higher per FDA standards.
- PFE (Particle Filtration Efficiency): Masks such as N95 and KN95 must filter 95% of 0.3-micron particles.
- VFE (Viral Filtration Efficiency): Used to assess PPE’s virus filtration capability, especially in healthcare settings.
Additionally, there are various quality certifications such as NIOSH, CE, ASTM, etc. However, not all products require the same certifications—it depends on the specific product and its target market.
Common Quality Issues Leading to PPE Rejection:
Failure to meet bacterial filtration standards (BFE, PFE, VFE)
Beyond bacterial filtration capabilities, PPE materials must also meet durability standards, ensure user safety, and provide protection against hazardous factors. Common material-related PPE defects include:
- Medical gloves: Prone to tearing, poor elasticity, talc powder causing skin irritation.
- Protective gowns: Non-waterproof, easily torn, failing ASTM or EN standards.
- Masks: Thin filter layers, easily torn, causing discomfort during extended use.
Example:
The U.S. Food and Drug Administration (FDA) issued Import Alert 80-04, which allows immediate detention without physical inspection for surgical and examination gloves from manufacturers failing to meet quality standards.
Many manufacturers and suppliers from Canada, China, Malaysia, and other countries have failed to provide medical gloves of adequate quality for U.S. distribution. Defective gloves pose risks to both users and patients.
Lack of Proper Certification and Licensing
PPE imported into the U.S. must have valid certification before being allowed for distribution. Failure to obtain the necessary licenses can result in shipments being held at ports or returned to the exporting country.
Required Certifications:
- FDA 510(k): Required for medical devices such as masks, gloves, and protective gowns.
- NIOSH Certification: Mandatory for N95 masks to ensure protection standards.
- CE Marking (Optional): European certification that enhances credibility but does not replace FDA certification.
- Independent Lab Testing: Verification from organizations such as UL, SGS, or Nelson Labs.
Common Certification Errors:
- Lack of NIOSH or FDA 510(k) certification
- Missing quality testing reports: Some PPE lacks independent lab test documents proving compliance, leading CBP and FDA to suspect product quality and reject clearance.
- Using outdated or expired FDA 510(k) certifications
- Misuse of certifications: Some companies use certification for one product but apply it to another PPE type, leading to rejection by CBP and FDA.
Labeling Issues
Compliance with labeling and customs import regulations is crucial to ensuring smooth clearance of goods into the United States. Below are common labeling issues that may cause PPE shipments to be rejected or held at ports:
One of the most common reasons for PPE import rejection in the U.S. is non-compliance with labeling regulations. Many shipments are held due to missing critical information, such as manufacturer details, country of origin, or usage instructions. For certified products, the absence of an FDA registration number or NIOSH certification code can also lead to rejection.
Additionally, improper language usage is a serious violation. If labels are printed only in a foreign language without an accompanying English version, or if incorrect translations misrepresent the product’s intended use, customs authorities may detain or reject the shipment.
Another issue is misleading or incorrect labeling. Some products are marketed with exaggerated claims that do not match their actual performance. For example, a mask with only 80% filtration efficiency being labeled as N95 (which requires a minimum of 95% efficiency) violates import regulations and can pose safety risks for users.
Finally, failure to comply with FDA and CBP labeling formats can also result in goods being blocked at the port. Common mistakes include missing batch numbers, lack of traceability, or missing required safety warnings and usage instructions. To avoid these risks, businesses must thoroughly inspect labeling before export, ensuring full compliance with FDA and CBP regulations.
Customs Import Issues
Beyond labeling issues, customs procedures pose another major barrier for PPE imports into the U.S. The CBP (Customs and Border Protection) has the authority to hold, deny clearance, or even destroy shipments that fail to comply with regulations.
Errors or Missing Information in Import Documents
U.S. regulatory agencies require import documents to be accurate, transparent, and complete. Even minor errors, such as incorrect quantities, discrepancies between documentation and actual shipments, unclear product descriptions, typographical errors, or missing certification documents, can result in delays or outright rejection.
If businesses fail to promptly correct or supplement these errors, goods may be held in storage at the port, leading to high warehousing costs or even being returned to the exporting country.
Failure to Pre-Register with the FDA
Companies exporting PPE to the U.S. must register with the FDA before shipping. Failure to do so will result in shipments being held at the port.
- The FDA requires all manufacturers and exporters of PPE to pre-register and obtain an FDA Establishment Registration Number.
- If a business fails to register or does not renew its registration on time, shipments may be denied entry or face prolonged processing, causing significant business disruptions.
Tariff and Customs Duty Issues
Some companies fail to accurately declare the Harmonized Tariff Schedule (HTS) code for PPE, leading to shipment holds for additional verification.
- The HTS code is a tariff classification system used to determine duty rates and import regulations. If a company misclassifies a product, CBP may detain the shipment for further investigation into its legality.
- Some businesses intentionally misdeclare the HTS code to benefit from lower tariffs, but this can result in penalties, fines, or even a future import ban.
Solutions to Ensure PPE Shipments Are Accepted by the U.S.
To avoid import rejection in the U.S., PPE exporters must strictly comply with quality standards, complete legal documentation, and ensure proper shipping procedures. Below are specific measures to address common issues:
Ensure Product Quality Meets U.S. Standards
The U.S. has strict requirements for PPE to protect users. Therefore, for PPE to be accepted into the U.S. market, products must comply with the stringent FDA, CDC, and NIOSH standards. Specifically:
- For medical masks: Must meet Bacterial Filtration Efficiency (BFE), Particle Filtration Efficiency (PFE), and Viral Filtration Efficiency (VFE) as per FDA standards.
- For protective masks (N95): Must have NIOSH certification.
- For medical gloves and protective gowns: Must comply with durability, tear resistance, and chemical resistance requirements.
To ensure compliance, businesses should collaborate with FDA-approved independent laboratories for quality testing. This helps verify that the products can pass rigorous tests before export.
Additionally, quality control throughout the manufacturing process is crucial. Implementing a quality management system in accordance with ISO 13485 standards (for medical devices) ensures product consistency and safety. At the same time, businesses must strictly monitor raw material sourcing, avoiding low-quality materials to minimize the risk of import rejection.
Complete Certification and Licensing Documents
Lack of proper documentation is one of the main reasons PPE shipments are rejected by U.S. authorities. To avoid this risk, businesses must prepare all required certifications, including:
- FDA 510(k): Required for medical masks, gloves, and protective equipment.
- NIOSH Certification: Mandatory for N95 masks.
- Independent lab testing reports: To prove product quality compliance.
Moreover, regularly reviewing and updating documentation is crucial. Businesses must ensure that all certifications remain valid, error-free, and properly formatted. Additionally, pre-registering with the FDA helps prevent shipments from being held at ports, reducing the risk of export delays.
Comply with Labeling and Customs Import Regulations
PPE product labeling for U.S. imports must meet strict requirements; otherwise, shipments may be held at ports or denied entry. To avoid these risks, businesses must adhere to the U.S. labeling requirements for PPE, including:
- Language: Labels must be in English.
- Manufacturer Information: Must include the name, address, and country of origin.
- Product Description: Clearly specify the PPE type (e.g., masks, gloves, protective gowns).
- Usage Instructions: Provide guidance on proper use, intended users, and any restrictions.
- Safety Warnings: Indicate any potential risks, allergic reactions, or incompatibility with medical environments.
- Certification and Registration Number: If regulated by the FDA, labels must display an FDA registration number or NIOSH certification (for N95 masks).
- Batch Number and Manufacturing Date: Essential for traceability in case of quality concerns.
Additionally, businesses must carefully inspect all labels before export to ensure full compliance with FDA and CBP regulations, allowing for smooth customs clearance and avoiding unnecessary losses.
Select a Reliable Logistics Partner and Control Export Processes
Choosing an experienced logistics provider for PPE exports to the U.S. is crucial in mitigating customs-related risks. A professional logistics company will:
- Understand U.S. import procedures and FDA/CBP compliance requirements.
- Efficiently handle paperwork and certifications, ensuring fast customs clearance.
Additionally, businesses must strictly monitor the export process by:
- Verifying all documentation before shipment to avoid errors.
- Conducting pre-customs inspections to minimize the risk of shipment holds at U.S. ports.
- Ensuring compliance with transport regulations to prevent delays and financial losses.
Stay Updated on U.S. Regulatory Changes
U.S. PPE import regulations change frequently, especially during public health crises and increasing protective equipment demand.
- Regularly check updates from the FDA, CBP, and other regulatory bodies.
- Consult export compliance experts to ensure continuous adherence to U.S. standards.
- Participate in industry workshops and training programs to stay informed about the latest PPE export requirements.
Conclusion
Exporting personal protective equipment (PPE) to the U.S. presents significant business opportunities but also comes with major challenges due to strict regulatory controls. The most common reasons PPE shipments are rejected include:
- Failure to meet quality standards
- Lack of proper certifications and documentation
- Non-compliance with labeling and customs import regulations
These issues not only result in financial losses but also damage a company’s reputation in the international market.
To ensure successful PPE imports into the U.S., businesses must:
- Ensure product quality meets U.S. standards as required by FDA, NIOSH, and other regulatory agencies.
- Complete all necessary documentation and certifications before export to prevent rejections at U.S. ports.
- Strictly adhere to labeling and customs regulations, including accurate product information, manufacturer details, and valid registration numbers.
- Stay updated on the latest regulatory changes to minimize risks and optimize export processes.
📢 Key Advice: PPE exporters should collaborate with compliance experts, independent testing agencies, and ensure full adherence to U.S. standards before shipping. This not only facilitates smooth customs clearance but also enhances competitiveness in the global market.
Call to Action
As U.S. PPE import regulations become increasingly strict, TM&DV 8688 COMPANY LIMITED has successfully established its position in the market by exporting PPE to the U.S. Through strict adherence to quality standards and rigorous inspection processes, the company has demonstrated strong manufacturing and export capabilities.
The success of TM&DV 8688 COMPANY LIMITED serves as clear proof that compliance with regulations and quality assurance are key factors in ensuring PPE shipments enter the U.S. market smoothly. This experience provides valuable insights for Vietnamese businesses aiming to penetrate such a highly regulated and competitive market.
📢 Contact us today for expert consultation and to purchase certified PPE that meets all quality and export requirements!